Streamlining Operations for a Mid-Sized Manufacturing Company
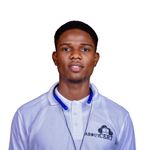
Case Study: Streamlining Operations for a Mid-Sized Manufacturing Company
Disclaimer: This is a hypothetical case study created for illustrative purposes to demonstrate the types of solutions our company can provide. Any resemblance to real companies or situations is purely coincidental.
Client:
ABC Manufacturing, a mid-sized company producing custom machinery parts for various industries, including automotive, aerospace, and consumer electronics.
Industry:
Manufacturing
Challenge:
ABC Manufacturing was struggling with inefficiencies in their operations that were significantly impacting their business. Key issues included:
Delayed Production Schedules: Frequent delays in production were causing missed deadlines and strained relationships with clients.
High Operational Costs: Inefficiencies and waste in the production process were driving up operational costs, affecting profitability.
Inaccurate Inventory Management: Poor inventory tracking led to stockouts and overstocking, disrupting the production flow.
Low Employee Productivity: Outdated systems and manual processes were causing low productivity and high error rates among employees.
Objective:
To streamline ABC Manufacturing’s operations by:
Modernizing their systems
Improving inventory management
Enhancing overall productivity
Reducing operational costs
Solution:
1. ERP System Implementation:
Analysis: Conducted a thorough analysis of ABC Manufacturing’s existing operational processes, identifying key areas of inefficiency.
Selection: Selected a robust Enterprise Resource Planning (ERP) system tailored to the manufacturing industry, capable of integrating various facets of the business including production, inventory, sales, and HR.
Customization: Customized the ERP system to meet the specific needs of ABC Manufacturing, ensuring it addressed their unique challenges and workflows.
Training: Conducted comprehensive training sessions for employees to ensure they were well-versed in using the new system, which included modules on production planning, inventory management, and order processing.
2. Inventory Management Optimization:
Real-Time Tracking: Implemented a real-time inventory tracking system integrated with the ERP, providing accurate and up-to-date inventory data.
Automated Alerts: Set up automated stock replenishment alerts to notify the purchasing department when inventory levels were low, preventing stockouts.
Forecasting: Developed a more accurate inventory forecasting model using historical data and market trends, helping to predict future inventory needs more precisely.
Barcoding: Introduced a barcoding system for all inventory items, which improved tracking accuracy and reduced manual entry errors.
3. Production Schedule Enhancement:
Dynamic Scheduling: Utilized the ERP system to create dynamic and flexible production schedules that could adapt to changing demands and priorities.
Workflow Management: Implemented a workflow management system to monitor progress in real-time, identify bottlenecks, and ensure timely completion of production tasks.
Feedback Loop: Established a feedback loop where production data was regularly reviewed to identify areas for improvement, allowing for continuous optimization of the production process.
4. Employee Productivity Improvement:
User-Friendly Interfaces: Integrated user-friendly interfaces and mobile applications for shop floor workers, making it easier for them to access information and complete tasks efficiently.
Automation: Automated routine and repetitive tasks such as data entry and reporting, freeing up employees to focus on more value-added activities.
Ongoing Training: Provided ongoing training and support to ensure staff could fully leverage the new systems and technologies, enhancing their productivity and reducing error rates.
Results:
The implementation of these solutions led to significant improvements in ABC Manufacturing’s operations:
Production Schedules: Achieved a 30% reduction in production delays, ensuring on-time delivery of products and improving client satisfaction.
Operational Costs: Decreased by 20% due to improved efficiency, reduced waste, and optimized use of resources.
Inventory Accuracy: Improved by 40%, leading to better stock management, fewer production disruptions, and more efficient use of working capital.
Employee Productivity: Increased by 25%, as employees could focus on more critical tasks and make better use of their time and skills.
Conclusion:
Our collaboration with ABC Manufacturing demonstrates our ability to modernize and optimize manufacturing operations. By implementing an integrated ERP system, optimizing inventory management, and enhancing employee productivity, we were able to significantly improve operational efficiency and reduce costs. This case study exemplifies our capability to deliver tailored solutions that drive tangible results for our clients in the manufacturing sector. Our comprehensive approach ensures that businesses can meet and exceed their operational goals, leading to sustained growth and competitiveness in the market.
Other Case Studies
HAVE SOMETHING IN MIND?
WHEN DO WE START,
CONNECT WITH US TODAY
Your strategic partners in software solutions, development, engineering, consultancy, and training.